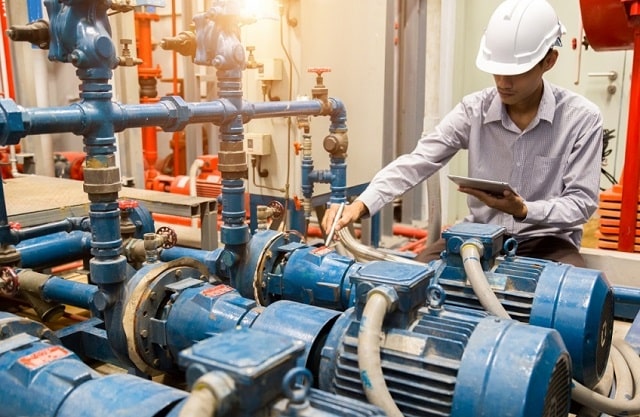
Key Takeaways
- Insight into the vast array of industrial pumps and their specialized applications across various sectors.
- An exploration of the intersection between technological advancements and pump efficiency.
- Guidance on establishing effective maintenance plans, reducing energy consumption, and adhering to pump safety protocols.
Table of Contents
- Introduction to Industrial Pumps
- Different Types of Industrial Pumps and Their Applications
- The Evolution and Advances in Pump Technology
- Factors Influencing Pump Selection in Manufacturing
- Maintenance Strategies for Industrial Pumps
- Energy Efficiency and Sustainability in Pump Operations
- Cost Considerations and Lifecycle Management of Pumps
- The Impact of Industrial Pumps on Product Quality Control
- Safety and Compliance Considerations in Pump Usage
- Future Trends in Pump Engineering and Application
Introduction to Industrial Pumps
Industrial pumps are essential components of many manufacturing systems and are used in various industries, including pharmaceuticals and agriculture, as lifelines. Through their capability of transferring various fluids and gases, these pumps ensure the continuity of processes and the quality and safety of the products being manufactured. Due to their widespread usage and critical functions, there is a pressing need for industry players to have a deep understanding of pump technology, their operational mechanisms, and the criteria for selecting the right pump to meet the application requirements effectively.
While industrial pumps are generally perceived as simple machines, their impact on production efficiency and cost-effectiveness is monumental. An optimized pump selection can lead to significant energy savings and low maintenance costs, further underscoring their financial impact on a business operation. The correct pump, in perfect working condition, can streamline workflows, safeguard product quality, and minimize risks associated with equipment failure.
Different Types of Industrial Pumps and Their Applications
Each type of industrial pump is designed to handle specific tasks tailored to the conditions in which they will be operating and the type of material they will be moving. Centrifugal pumps utilize a rotating impeller to impart kinetic energy to the fluid, making them ideal for handling low-viscosity fluids such as water or chemicals in large volumes. Positive displacement pumps, in contrast, work by trapping a fixed amount of fluid and then displacing that volume into the discharge pipe, which suits them for tasks that require high levels of precision and are perfect for thicker or more viscous fluids or those containing solid suspensions.
Delving deeper, specific varieties such as diaphragm pumps are distinguished using a flexible diaphragm to pump the fluid. They are frequently employed in sectors like food and beverage production and pharmaceuticals, where sanitation is crucial. Gear pumps, another form of positive displacement pump, employ interlocking gears to pump fluid; they are commonly found within machinery lubrication systems. Each pump type has an application niche where it excels, and its proper deployment is crucial for achieving efficient system performance.
The Evolution and Advances in Pump Technology
As industries have advanced, so too has pump design and functionality. Initially focused on straightforward mechanical operation, modern pumps have embraced technological enhancements that offer far-reaching benefits. Innovations in the materials used to construct pumps, for instance, have increased resistance to wear and corrosion, thus extending the pumps' lifespan even under harsh industrial conditions.
Another significant influence is the digital revolution. Pumps today, including those found within the inventory selections at places, are increasingly equipped with sensors that provide critical real-time data on performance and potential faults. By enabling predictive maintenance techniques, potential problems can be found and fixed before they result in system failures, reducing unscheduled downtime and related expenses.
Factors Influencing Pump Selection in Manufacturing
The pursuit of the ideal pump for a system necessitates a comprehensive evaluation of numerous variables. The primary factor influencing the pump selection is the particular properties of the material to be moved, whether it be a liquid, gas, or slurry. It includes assessing factors such as fluid viscosity, which significantly influences the pumping mechanism required, and chemical compatibility, which is critical for ensuring materials within the pump can withstand prolonged exposure to aggressive substances without degrading. As with safety, environmental factors like operating temperature ranges and possible exposure to explosive environments must be considered to avoid malfunctions and guarantee safety.
Maintenance Strategies for Industrial Pumps
A robust maintenance regimen is the backbone of reliable pump operations. Proactive strategies are vital. It can include the analysis of vibration patterns, temperature fluctuations, or changes in the acoustic signatures that could indicate developing faults. Trained personnel are an integral part of a successful maintenance strategy, as their expertise enables them to pinpoint issues before they lead to catastrophic failures. Best practices recommend a blend of routine inspections and more in-depth analyses for the most effective maintenance, such as performance testing or fluid analysis. These comprehensive approaches provide a complete understanding of the pump's condition and operational efficacy, contributing to an extended service life and a more reliable manufacturing process.
Energy Efficiency and Sustainability in Pump Operations
The pursuit of operational excellence in manufacturing is closely tied to energy efficiency, particularly when it comes to pump operations. Enhancing the energy efficiency of pumps is frequently a top priority because they can account for a sizeable amount of a facility's energy consumption. Optimization techniques can have a significant impact. Advanced control systems are also being integrated, allowing dynamic pump speed or flow adjustments to match real-time demand, thus eliminating wasted energy. The move towards greener and more sustainable operations is also influencing pump technology. Some manufacturers are focusing on developing more environmentally friendly pumps by using renewable energy sources or designing pumps that can be easily refurbished or recycled at the end of their useful life, thereby reducing waste and contributing to the circular economy.
Cost Considerations and Lifecycle Management of Pumps
Factoring in the total lifespan costs of industrial pumps, rather than just the initial purchase price, is a critical approach for businesses. Evaluating the long-term costs encompasses assessing energy consumption over time, maintenance expenses, and the potential costs associated with downtime. A lifecycle management plan for pumps helps operators predict when maintenance or replacements will be needed, allowing for budget planning and ensuring operations run without unexpected interruptions.
The Impact of Industrial Pumps on Product Quality Control
Failure to maintain pumps properly or select the appropriate pump type can harm product quality. In industries where precision and cleanliness are non-negotiable, such as the pharmaceutical sector, even minor inconsistencies in pump performance can compromise product integrity and contravene industry regulations. Consistent and predictable pump operation is a cornerstone of maintaining product standards and meeting rigorous quality control measures.
Safety and Compliance Considerations in Pump Usage
Industrial pump operations often involve handling hazardous materials, high pressures, and temperatures, giving rise to several safety concerns. It is imperative that companies institute rigorous safety protocols and routinely train their workforce on proper operational procedures. Compliance with industry standards and regulations is not optional; it is a legal and moral requirement to protect workers and the environment. By understanding and adhering to guidelines and best practices issued by organizations like OSHA, businesses can prevent accidents and avoid costly violations.
Future Trends in Pump Engineering and Application
The horizon of pump engineering is brimming with potential, offering a glimpse into a future where pump efficiency, intelligence, and performance are significantly enhanced. Anticipated developments in materials allow pumps to operate in more extreme conditions with excellent resistance to wear, corrosion, and high temperatures. The potential for custom pump designs that precisely match specific system requirements with lower production costs and shorter lead times may be facilitated by advancements in additive manufacturing, also referred to as 3D printing.
Integrating pumps with advanced analytics and machine learning algorithms is expected to bring about a new generation of smart pumps capable of autonomous decision-making to optimize performance and energy usage. Thanks to their operational excellence insights, these intelligent systems will likely become standard as Industry 4.0 continues to evolve. The future trends in pump engineering paint a picture of a sector that is not only essential to manufacturing processes but also actively pushing the boundaries of industrial innovation.